製造ライン機器の設計・製造・メンテナンス
信頼性の高いフルオーダーメイドの製品をワンストップで。
当社は主に自動車部品の製造ラインを手掛けており、フルオーダーメイドによる設計や製造はもちろん、製品のメンテナンスまでをワンストップで承ることが可能です。
また、最新の設備を積極的に導入することで、高度な加工技術を発揮するほか、コスト低減と短納期を実現しています。
創業から40年以上にわたり培ってきた技術力・対応力で、お客様のニーズに合った、より良い製品とサービスをご提供します。
各種専用機の治具や装置の設計・製造
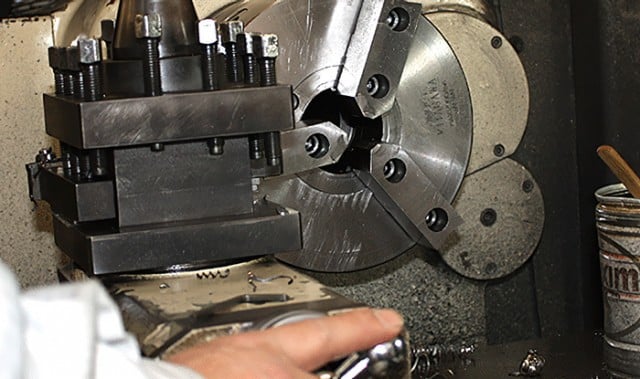
企画の段階から打ち合わせを行い、お客様のニーズに合わせたものを形にします。
製造から組立・制御まで、自社工場だけでなく派遣業務での組立作業も行っています。
各種精密部品の加工

フライス加工や旋盤加工、研磨加工(平研・円筒研磨)、マシニング加工などに対応し、各種精密部品をあらゆる形状に加工します。
バーコード管理システムの活用
バーコード管理システムとは、製造ラインで個々の製品にバーコードを貼付し、製造・出荷・設置の状況を一貫してデータベースで管理するシステムです。
バーコードを利用することで、正確な検品や入出荷報告などの各種作業をマルチにカバーし、誤出荷の防止と製品トレーサビリティを確保します。
また、手間のかかる物流業務を簡略化・正確化・迅速化することによって、納期までのスピードアップを実現し、顧客満足度の向上につながります。
製品出荷までの流れ
Step1. お客様からのオーダー

お客様からのオーダーを受け、打ち合わせにて製品仕様を決定します。
Step2. 設計
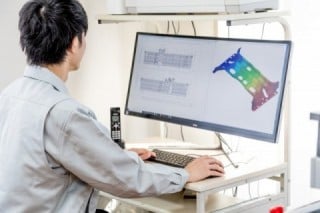
打ち合わせの内容をもとに、CADを用いて設計を行います。
Step3. 加工

設計書をもとに、切削や研磨などの部品加工を行います。
Step4. 組立・調整
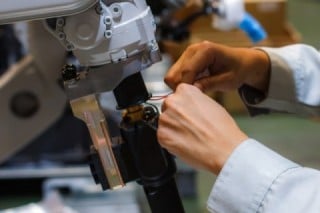
お客様から支給いただいた部材で組立・調整を行います。
Step5. 電気制御
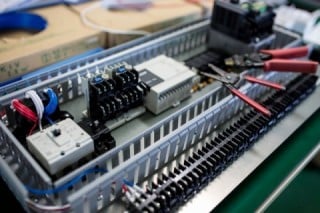
電気制御プログラムを入力し、お客様の設備内で動作確認を行います。
Step6. お客様立ち会い
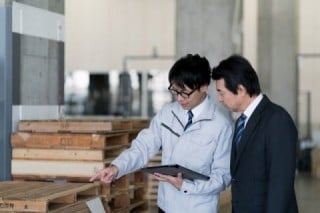
お客様立ち会いの下で、製品が仕様どおりに動作するか試運転を行います。
Step7. 出荷
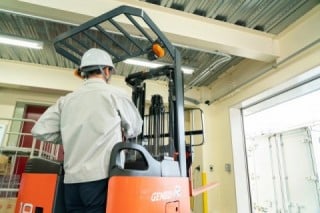
お客様から承認いただいた後、製品をご指定の場所へ出荷します。
Step8. アフターサポート
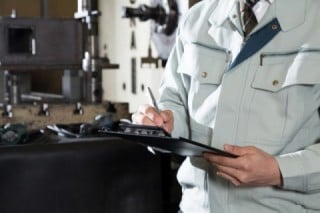
状況に応じて製品のメンテナンスを実施します。